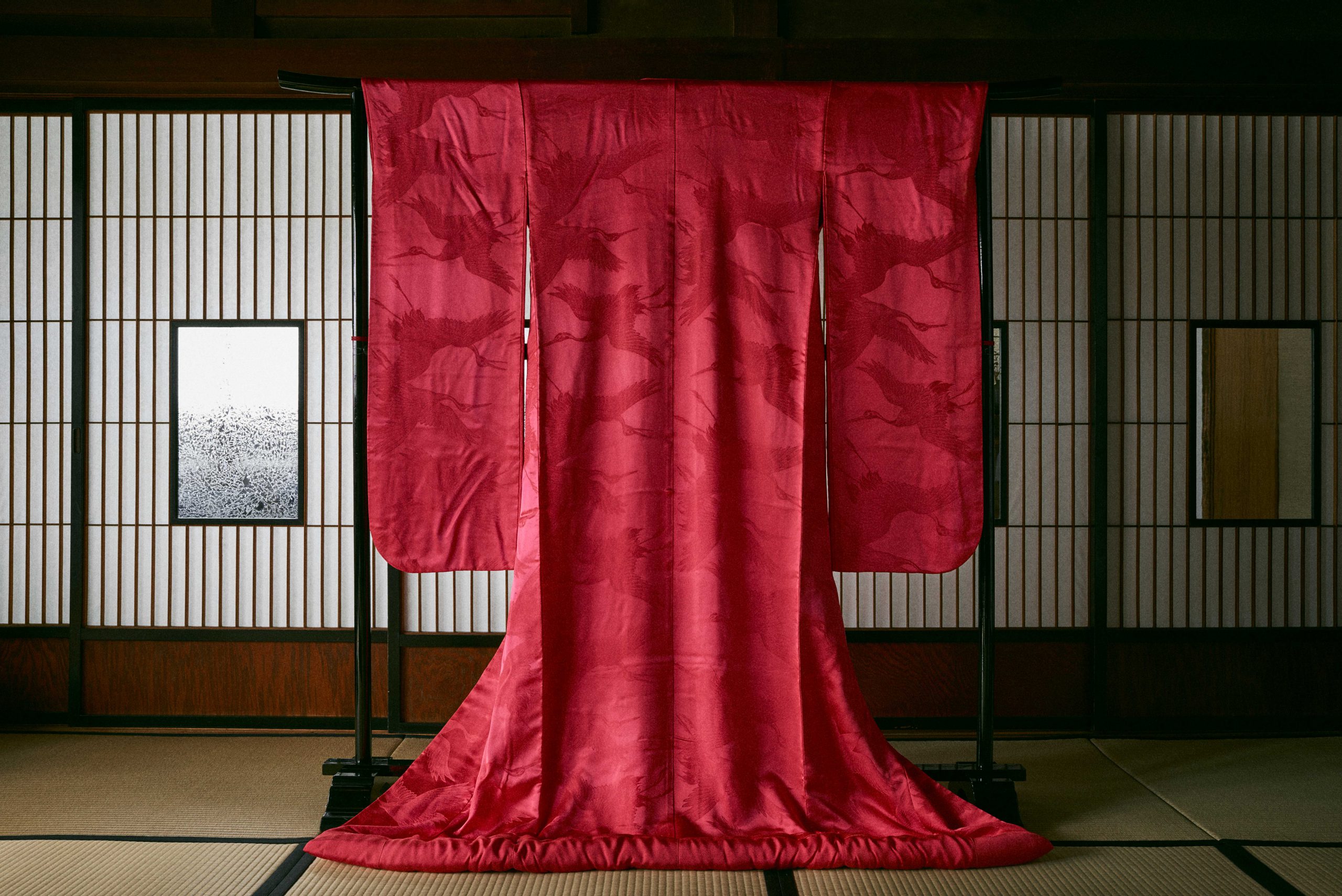
The Story of Japanese Textiles
Benibana-zome
The Story of Japanese Textiles
Ai-zome
Hosoo was founded in 1688 and, for many years since, operated as a weaver. In 1923, the 9th head of the family, Tokujiro Hosoo, started the wholesale business of obi and kimono.
Today, the wholesale business has expanded and includes the curation of kimono culture and dyeing and weaving culture. As a curator, we research how dyeing and weaving cultures throughout Japan are interconnected and communicates the findings through our gallery and showroom.
Starting in 2015, we spent four years traveling from Hokkaido to Okinawa to visit 33 production sites of dyeing and weaving and to record the local culture nurtured by history and land. What we have learned ranges from each location’s natural environment, dyeing and weaving production process, people involved in dyeing, to unique materials and tools. Each of these elements contains a story about their local dyeing and weaving culture. So far, we have taken and archived over 20,000 photographs.
Tadeai (Persicaria tinctoria) in the buckwheat family, indoai (Indigofera su ruticosa) of the genus Indigofera in the pea family, Ryukyuai (Strobilanthes cusia) in the Acanthus family, and woad (Isatis tinctoria) in the mustard family-around the world, there exist techniques and cultures that use blue colorant “indigo” from various plants to dye fibers deep blue. Particularly in Japan, it is not an exaggeration to say that ai-zome (indigo dyeing) has been the most valued dyeing method since the spread of cotton farming in the early modern period. Atkinson, a chemist who came to Japan in the early Meiji period, was surprised to find so many Japanese people wearing blue garments and coined the term “Japan blue,” which is still in use today.
There are several methods for traditional ai-zome using tadeai, an annual plant of the genus Persicaria in the buckwheat family that used to be grown mainly in Honshu along the western part of the Pacific coast and in Shikoku and Kyushu, with its northern limit in the southern Tohoku region. The most popular is the aku-hakko-date (lye fermentation method).
Indigo, the colorant ingredient, is found in the leaf of tadeai as a transparent substance called “indican,” an indigo’s precursor. The leaves are harvested, dried, and fermented to produce indigo and then processed into preservable dye called sukumo. Because indigo does not dissolve in water or alcohol, to use it for dyeing, it needs to be fermented (a chemical change by microorganism action) again under an alkaline environment. By doing so, indigo is promoted to be transformed into water-soluble leuco indigo, which is applied to fibers and then exposed to the air to dye the fibers blue. The aku-hakko-date, which requires fermentation twice, is a technique unique to Japan. It fixes color well, and even when the dyed fibers are run through water multiple times, its color does not fade or migrate.
In the late Edo period, when the indigo dyeing was widely practiced, Awa Province (Tokushima Prefecture) produced the best, in quality and amount, ai (indigo dye) and sukumo. This is made possible by Awa’s fertile soil brought about by the flooding of the Yoshino River and long hours of sunshine. In anticipation of the flooding of the violent river known as Shikoku Saburo, the northern bank, where the indigo fields spread, was purposely built lower than the southern bank, where the castle town was located. At the house of Akihito Sato, who still produces sukumo in Awa no Kitagata (northern part of Awa), an evacuation boat is hung from the eaves, the tradition inherited by the family of sukumo makers.
The production of sukumo, which is still continued under Mr. Sato’s guidance, begins with the sowing of tadeai in early March and lasts for about ten months. The resulting sukumo is mixed with alkaline lye, bran and sake which become a nutritious source during fermentation, and wait to be fermented in a vat. As the fermentation progresses at a temperature between 25 and 30 degrees Celsius, tiny air bubbles form on the surface. This phenomenon, described as the “blooming of indigo,” is used as a way to judge the subtle condition of fermentation.
When soaking a yarn or cloth into the dye, the indigo-colored liquid briefly takes on a deep green color with a hint of gold. However, as soon as the tread or cloth is lifted and exposed to the air, the fibers instantly turn deep indigo.
About three or four months after planting tadeai, the first crop is harvested during the rainy season between late June and early July. After that, the sun-dried leaves are finely cut and stored. After nedoko (bed) is created, the fermenting process of the leaves (nesekomi) begins in early September, followed by a process of turning the leaves over (kirikaeshi). Just as toji (chief brewer) is responsible for making sake, ai-shi (indigo dye master) is in charge of the entire process of making sukumo. Ai-shi assesses the state of fermentation by looking at the condition of the tadeai, which has varying qualities from year to year, and makes precise judgments about the timing of kirikaeshi, which takes place 20 to 22 times in about 100 days, the amount of water, and the height of the pile. What influences the judgments are the smell, viscosity, and weight of the leaves. To understand the degree of fermentation and give correct instructions to the workmen, the ai-shi must hone the five senses and have many years of experience. Akihito Sato laughingly says that the secret is “to listen to the indigo’s voice. It sometimes resists, and other times it fights back. It’s like raising a child.”