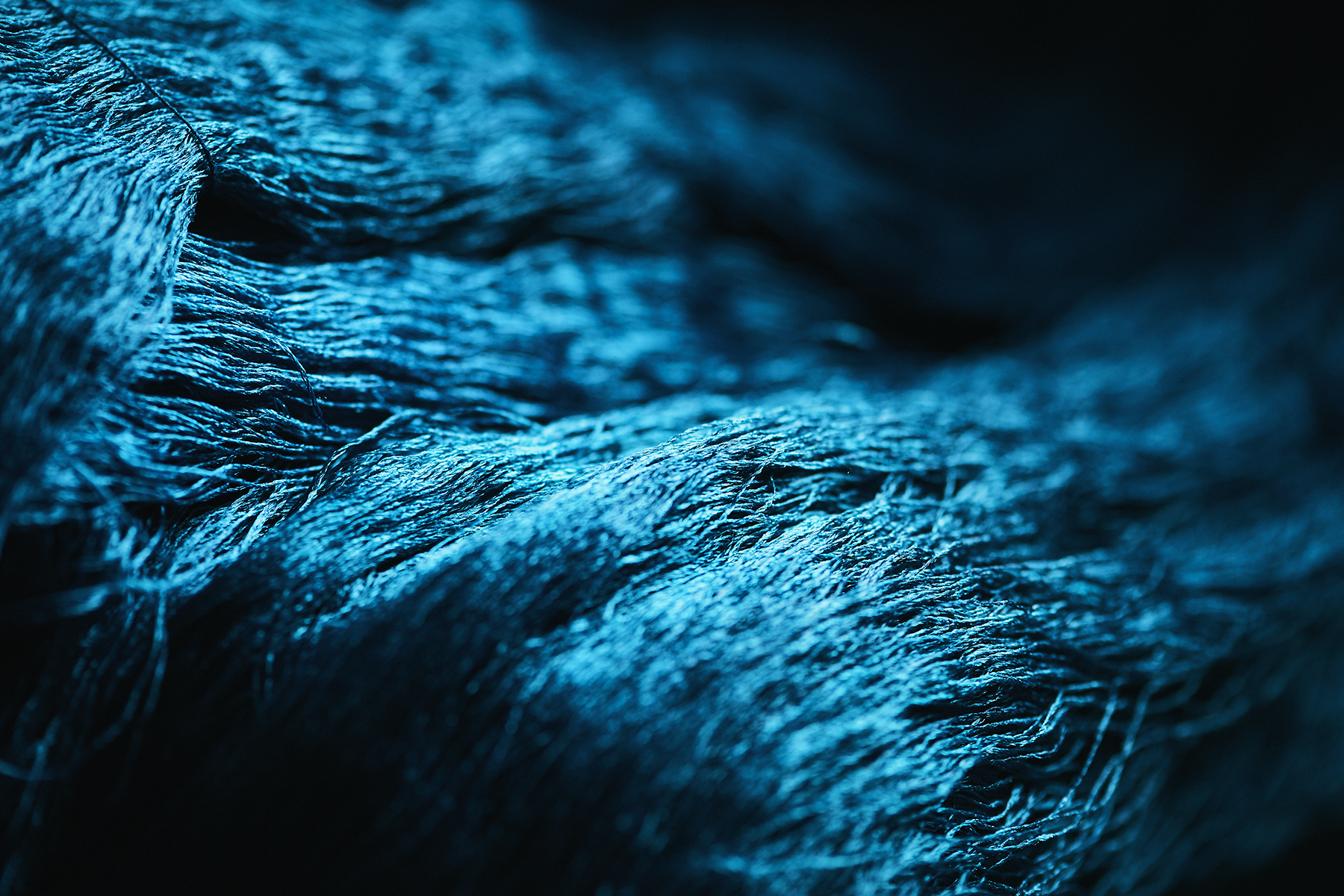
The Story of Japanese Textiles
Ai-zome
The Story of Japanese Textiles
Benibana-zome
Hosoo was founded in 1688 and, for many years since, operated as a weaver. In 1923, the 9th head of the family, Tokujiro Hosoo, started the wholesale business of obi and kimono.
Today, the wholesale business has expanded and includes the curation of kimono culture and dyeing and weaving culture. As a curator, we research how dyeing and weaving cultures throughout Japan are interconnected and communicate the findings through our gallery and showroom.
Starting in 2015, we spent four years traveling from Hokkaido to Okinawa to visit 33 production sites of dyeing and weaving and to record the local culture nurtured by history and land. What we have learned ranges from each location’s natural environment, dyeing and weaving production process, people involved in dyeing and weaving, to unique materials and tools. Each of these elements contains a story about their local dyeing and weaving culture. So far, we have taken and archived over 20,000 photographs.
“If you were a safflower, I would dye my sleeves with it and carry it with me.” The waka poem from the Manyōshū [Collection of Ten Thousand Leaves] is one of the numerous examples found in Japanese classical literature that describe clothes in crimson color. In Japan, dye plants such as akane [madder], suō [sappan], and benibana [safflower] have been used to produce different types of red—red, vermilion, crimson, cinnabar, scarlet—, but the red from safflower has been known to be
particularly vivid.
Benibana-zome [safflower dyeing] uses petals of safflower, a plant in the genus Carthamus of the family Asteraceae. Safflower-dyed cloths have been excavated at ancient sites in Egypt, and safflower seeds have been discovered at Mesopotamian ruins. The timing of its introduction to Japan, via the Silk Road, is estimated to be somewhere between the third century and the fifth to sixth century. There are records of safflower cultivation in various parts of the country from at least
as early as the Heian period.
Safflower had been highly valued not only as a dye ingredient but also as cosmetics such as lip and cheek colors and a natural drug, and its seed produced vegetable oil. In the basin of the modern-day Mogami River, Yamagata Prefecture, safflower cultivation began toward the end of the Muromachi
period, and by the Edo period, the area had become a major production site of high-quality safflower. The safflower shipped to Kyoto from Sakata via the Mogami River was called Mogami-benibana, accounting for about 60% of the country’s total production. The cosmetic rouge extracted from safflower was so expensive that the phrase “beni ichimonme, kin ichimonme” [an ounce of rouge equals an ounce of gold] was coined to describe its value.
However, the Meiji period saw a rapid decline in Mogami-benibana production due to the imports from overseas, the spread of chemical dyes, and food shortages, resulting in the loss of the safflower dyeing technique practiced mainly in Kyoto.
The person who took on the task of reviving this technique was Takao Suzuki, a science teacher at a junior high school in Yonezawa and a dye researcher. As he made attempts at the restoration, he asked Nitta, a textile manufacturer belonging to the family of his former student, for cooperation. In the end, the third-generation head of the company, Hidetsugu Nitta, and his wife Tomiko jointly brought back the detailed technique of safflower dyeing and succeeded in recreating benibana-zome textile.
The photos (above) depict a crimson uchikake [outer robe] made of safflower- dyed satin fabric. It was produced by Nitta, which began in 1884 as a weaving shop in Yonezawa, Yamagata Prefecture. The robe was worn as a wedding dress by the sisters of Gentaro Nitta, the fifth-generation and current head of the company. The garment also adorned his wife, Mayumi, at their wedding.
According to Mr. Nitta, a safflower-dyed textile is distinct in that it exhibits deep coloring imbued with light not only in bright light but also in darkness, causing the color to glow. The rich luster makes one imagine how beautiful the textile would have looked in subdued light from candles and paper lanterns in old times.
Safflower, which is also Yamagata’s prefectural flower, produces thistle-like, yellowish red flowers in early to mid-July. Picking these flowers is the first step in safflower dyeing. The safflower flowers are entirely yellow when they start blooming, but with time, they turn slightly reddish. To process them as a dye, the best timing to pick them is when the flowers are in 80% full bloom, with the lower part of the petals turned red. As safflower has sharp prickles on the leaf ’s edge, it is harvested by hand in the early morning when the needles are softened and weighed down by morning dew.
A safflower petal contains two types of pigments: safflor yellow for yellow and carthamin for red. After harvesting the flower, petals are collected before the day is over and carefully washed under running water. Once the water is drained off, the petals are stomped on by feet (hanafumi) to damage the surface and laid out on a highly humid straw mat for fermentation, which causes the
petals to gradually turn red.
They are then pounded in a mortar, turning sticky and deeper red. The activity of carthamin synthase during this chemical process is finally beginning to be clarified in recent years.
Once the petals have turned crimson, they are rounded into balls by hand, placed between straw mats and stomped on with bare feet, and dried in a flat shape. These rice-cracker-like pieces, called benimochi [red cake] or hanamochi [flower cake], become the raw material for safflower dyeing.
They are light and easy to preserve and transport. During the Edo period, benimochi were transported to Kyoto via the Mogami River. Two kilograms of fresh safflower can produce only 200 grams of benimochi.
Benimochi are produced in midsummer and carefully preserved until the middle of winter. To use them for dyeing, they are soaked in water to squeeze out the remaining yellow pigment before extracting the dye liquor.
The basic principle of safflower dyeing is to remove the yellow pigment in petals as much as possible and effectively extract only the red pigment. To achieve this, the red pigment carthamin’s property of being insoluble in water but soluble in alkaline solution is exploited.
Alkaline lye is produced by making black straw ashes using imperfectly combusted rice straw, pouring hot water over the ashes, and, after a night, filtering the clear fluid at the top. When benimochi is soaked in the water mixed with the lye for a whole day and night, crimson pigment dissolves into the water. The technique of making benimochi from yellow petals of safflower and dyeing crimson with it had already been practiced during the Edo period. This technique contains the wisdom and ingenuity accumulated over many years.
The dye liquor, made by thoroughly squeezing a bag containing benimochi, is neutralized using rice vinegar and ubai (smoked ume plum abundant in citric acid) to stabilize the pigment. As soon as the yarn is soaked in the dye, it begins to turn crimson. It is important to constantly move the soaked yarn or cloth during dyeing because safflower dyeing tends to produce uneven color. To dye deep crimson, the dyeing process is repeated multiple times with new dye liquor each time to transfer, little by little, the crimson pigment to the yarn.
It is said that safflower dyeing produces the best result in the cold season. The saying derives from accumulated experience that, in summer, the dye liquor tends to change in quality, resulting in an impure color. There is also research that chemically supports this phenomenon with a published result showing that a dyed item turned bright crimson with no muddiness when the dye liquor’s temperature was below ten degrees Celsius at the time of dyeing.
The color of safflower dye liquor fades to almost transparent as yarn is repeatedly soaked and dyed. It is evident that every last drop of the precious crimson pigment is transferred to the yarn or cloth.
Safflower is also used as a natural drug, which is said to improve blood circulation. In the past, a safflower-dyed red cloth, called momi, was believed to cure eye diseases by wiping an eye with it. Furthermore, coupled with its appearance, safflower-dyed cloths are said to have a thermal insulation effect. The craftsmen who perform the dyeing process in the cold season also attest that, as long as they are touching the safflower dye liquor, their fingers don’t become numb even when
working in the snow.
Safflower-dyed yarn is thoroughly washed with water and dried in hanks. Depending on the number of times it is dyed, the resulting color varies from light pink to crimson to dark crimson. Safflower dyeing is often used to dye yarn, but it can also be used to dye undyed, satin-like silk fabric pictured at the beginning of this text. Today, weaving companies and workshops and dyeing and weaving artists who produce textiles using safflower-dyed yarn are concentrated in Yonezawa, Yamagata Prefecture.
Safflower dyeing was revived through the effort of Takao Suzuki and Hidetsugu and Tomiko Nitta in around 1960, and its production has continued since. At Nitta, they handle everything from harvesting safflower, dyeing yarn, dip-dyeing kimono textiles, to weaving, reflecting their philosophy that one must understand the nature of the raw materials to understand dyeing.